For new construction estimators, understanding quantity takeoff is critical to successful project planning and budgeting. Quantity takeoff (QTO) involves calculating the materials needed for a construction project and provides the foundation for accurate cost estimation, procurement, and scheduling. A solid grasp of QTO essentials will help new estimators avoid costly errors, manage resources effectively, and deliver reliable project estimates.
We’ll cover the essentials of quantity takeoff, including its importance, the tools needed, and key steps to achieve accuracy.
What is Quantity Takeoff in Construction?
Quantity takeoff (QTO) is the process of measuring and listing the materials, labor, and equipment required for a construction project. By analyzing architectural plans, blueprints, and project specifications, estimators determine the precise quantities needed for each resource. QTO is essential for budgeting, resource management, and procurement, making it a foundational skill for construction estimators.
Accurate quantity takeoff allows contractors to plan material orders, schedule deliveries, and keep projects on track. For new estimators, mastering quantity takeoff is crucial to delivering accurate project estimates and ensuring efficient resource allocation.
Why is Quantity Takeoff Important for New Estimators?
Quantity takeoff plays a vital role in construction estimating and project planning. Here’s why it’s essential for new estimators:
- Accurate Budgeting: Precise quantity takeoff enables accurate cost estimates, helping clients understand the budget requirements and making projects financially viable.
- Efficient Procurement: By calculating exact material quantities, estimators help procurement teams avoid overstocking or shortages, ensuring that the right resources are available when needed.
- Resource Management: QTO supports effective resource allocation, preventing delays and keeping projects on schedule.
- Minimizes Waste: Accurate takeoff reduces material waste, supporting sustainable construction practices and controlling costs.
Mastering QTO essentials is a valuable skill that helps new estimators make an immediate impact in their roles, contributing to project success and cost efficiency.
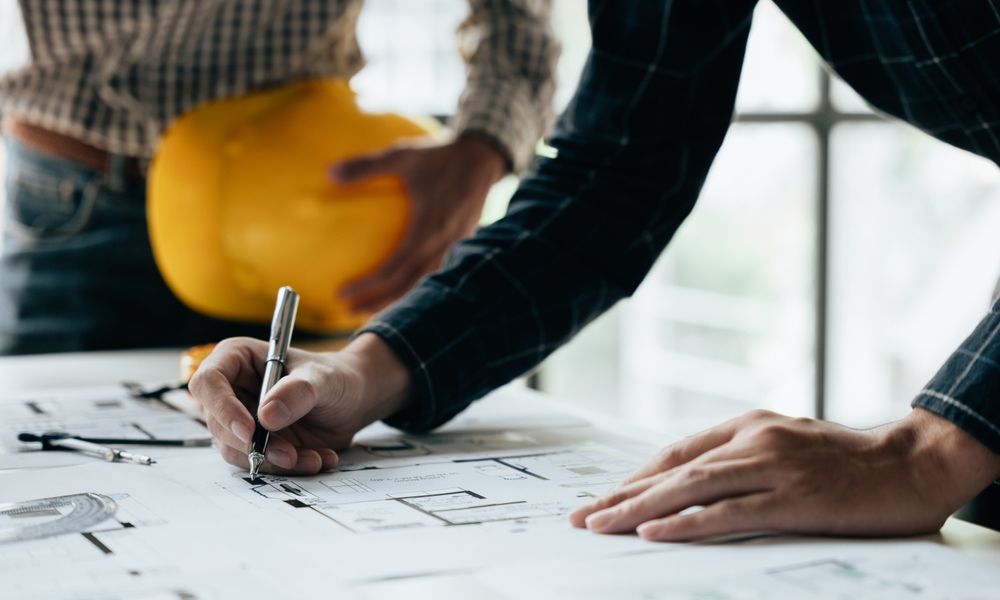
Essential Tools for Quantity Takeoff
To perform quantity takeoff accurately and efficiently, estimators rely on a combination of manual methods and digital tools. Here are some key tools every new estimator should know:
Digital Takeoff Software
Digital tools such as Bluebeam Revu, PlanSwift, and CostX streamline the takeoff process by automating measurements and calculations directly from digital drawings.
- Bluebeam Revu: Known for its PDF markup capabilities, Bluebeam allows users to measure dimensions, areas, and volumes on digital blueprints.
- PlanSwift: A user-friendly tool that enables fast measurements and integrates well with other estimating software.
- CostX: Designed for quantity surveyors, CostX offers advanced takeoff and cost estimation features, making it ideal for complex projects.
Scaled Rulers and Measurement Tools
For manual takeoff, scaled rulers, calipers, and other measurement tools are essential. These tools help estimators measure printed blueprints and convert dimensions into quantities. While manual methods can be time-consuming, they are useful for small projects or when digital tools are unavailable.
Estimating Spreadsheets
Spreadsheets allow estimators to organize, record, and calculate material quantities efficiently. Programs like Microsoft Excel provide formulas and templates for creating detailed takeoff sheets, which are easy to update and share with team members.
Key Steps for Accurate Quantity Takeoff
Performing accurate quantity takeoff requires a systematic approach. Follow these essential steps to ensure reliable results:
Step 1: Review Project Documents Thoroughly
Start by gathering all relevant project documents, including blueprints, engineering drawings, and specifications. Reviewing these documents carefully will help you understand the project scope, design details, and material requirements.
- Verify Document Versions: Ensure you’re working with the latest versions of all documents to avoid discrepancies.
- Identify Key Elements: Familiarize yourself with structural, architectural, and MEP (mechanical, electrical, plumbing) components to understand all material needs.
Step 2: Set Up Consistent Units of Measurement
Choosing consistent units of measurement is essential for accurate takeoff. This simplifies calculations and prevents errors during procurement.
- Standardize Units: Use cubic meters for concrete, square feet for drywall, and linear feet for piping.
- Match Supplier Standards: Align your units with those used by suppliers to avoid conversion issues during material ordering.
Step 3: Organize Materials by Categories
Organizing materials into categories streamlines the takeoff process, making it easier to track, review, and manage materials for each part of the project.
- Use Common Categories: Create categories such as structural, finishing, and MEP materials.
- Add Subcategories if Necessary: For complex projects, subcategorizing by material type, such as concrete, steel, or wood, enhances organization.
Step 4: Take Accurate Measurements
For each material, measure the required quantities directly from project plans. This can include a variety of measurement types depending on the material:
- Length: Use for materials like piping and wiring.
- Area: Calculate surface areas for materials such as flooring, drywall, or paint.
- Volume: Measure cubic volume for materials like concrete, ensuring depth and width accuracy.
Step 5: Account for Material Waste
Materials such as tiles, concrete, or lumber often require a buffer to account for waste due to cutting, fitting, or breakage. Without a waste allowance, you may run into material shortages.
- Include Waste Allowances: Add a buffer based on industry standards or past experience, typically 5-10% depending on the material.
- Adjust Based on Material Properties: Some materials require larger allowances, such as fragile or high-cutting-loss items.
Step 6: Document and Organize Quantities in Takeoff Sheets
An organized takeoff sheet enhances clarity and minimizes the risk of miscommunication. Record each material’s type, quantity, unit of measurement, and any relevant notes.
- Use a Consistent Format: Create a standardized template to ensure consistency across all takeoff sheets.
- Add Specifications and Notes: Include specific requirements, such as material grade or supplier preferences, for easier procurement.
Step 7: Cross-Check and Verify Quantities
Verification is essential to ensure accuracy in quantity takeoff. Even with digital tools, small errors can occur, impacting budgets and timelines.
- Peer Review: Have a colleague review your takeoff sheet to catch potential errors.
- Use Checklists for Completeness: Confirm that all materials, labor, and equipment needs are accounted for.
Step 8: Update Takeoff Sheets as Project Plans Change
Construction projects often undergo design changes or scope adjustments, impacting material requirements. Keeping takeoff sheets updated is crucial for maintaining accuracy in budgeting and procurement.
- Revise as Needed: Update your takeoff sheet whenever project details change to avoid ordering incorrect quantities.
- Notify Relevant Teams: Share updates with procurement and project managers to ensure everyone is aligned.
Best Practices for New Estimators
To enhance your quantity takeoff skills and deliver reliable estimates, follow these best practices:
- Start Small and Build Experience: Begin with smaller projects to practice your skills and build confidence.
- Leverage Digital Tools: Use digital takeoff tools for accuracy and efficiency, particularly on larger projects.
- Stay Organized: Keep takeoff sheets well-organized to prevent errors and simplify revisions.
- Collaborate with Colleagues: Engage with experienced team members who can provide guidance and feedback on your takeoffs.
Mastering quantity takeoff takes time and practice, but these best practices will help you develop strong estimating skills and deliver accurate results.
Conclusion
For new construction estimators, understanding quantity takeoff essentials is key to effective project planning, budgeting, and procurement. By following a structured approach, using the right tools, and adopting best practices, new estimators can produce accurate and reliable quantity takeoffs that support successful project outcomes.
Whether you’re measuring materials manually or using digital tools, honing your quantity takeoff skills is an invaluable investment in your career. By mastering the essentials, you’ll be well-equipped to tackle projects of all sizes and contribute to your team’s success.
Enhance Your Estimating Skills with Our Quantity Surveying Course
Want to master quantity takeoff and excel as a construction estimator? Our Online Quantity Surveying Course provides in-depth training on the essentials, from measurement techniques to digital tools. Gain the confidence and skills you need to deliver accurate estimates and support successful projects.Enroll Now in Our Quantity Surveying Course and start building your expertise in construction estimating!