In construction, performing a quantity takeoff (QTO) for complex structures is a critical skill that helps project managers, estimators, and quantity surveyors manage costs, schedule resources, and ensure projects remain on track.
Complex structures, like multi-story buildings, bridges, and industrial facilities, demand precise quantity calculations due to their large scale, multiple systems, and intricate design features. An accurate takeoff for these projects reduces errors, prevents material shortages or overages, and supports efficient project planning.
This guide provides a step-by-step approach to performing a quantity takeoff for complex structures, covering essential tools, best practices, and techniques that can enhance accuracy and streamline the process.
What is Quantity Takeoff?
Quantity takeoff is the process of identifying and measuring the materials, labor, and equipment required for a construction project. Estimators use architectural drawings, blueprints, and specifications to calculate material quantities, from concrete and steel to plumbing and HVAC components. These calculations are essential for budgeting, procurement, and project scheduling.
In complex structures, the quantity takeoff process involves additional considerations:
- Scale and Scope: Larger projects involve extensive quantities of materials and require precision to avoid excess waste or shortages.
- Complex Systems: Complex structures often incorporate multiple systems, such as HVAC, electrical, and plumbing, which require detailed measurements.
- Design Nuances: Complex buildings may have unique design elements or custom features that must be accounted for in the takeoff.
Tools for Performing Quantity Takeoff on Complex Structures
Using the right tools is crucial to ensuring accuracy and efficiency in quantity takeoff. Here are some tools essential for handling large-scale, complex structures:
Digital Takeoff Software
Digital tools like Bluebeam Revu, PlanSwift, and CostX allow estimators to perform measurements directly on digital blueprints, providing accuracy and reducing manual effort.
- Bluebeam Revu: Known for its robust measurement capabilities, Bluebeam Revu is ideal for measuring, annotating, and collaborating on complex projects.
- PlanSwift: PlanSwift is popular for its user-friendly interface and integration with other estimating tools.
- CostX: CostX offers advanced measurement features that are particularly useful for complex structures, with the ability to measure in 3D.
Scaled Rulers and Measurement Devices
While digital tools are preferred, scaled rulers, calipers, and laser measurement tools can assist in verifying measurements or handling elements of smaller scale on complex projects.
Estimating Software and Spreadsheets
Programs like Excel are useful for documenting, organizing, and calculating quantities. Custom templates for takeoff sheets ensure consistency across projects and improve readability.
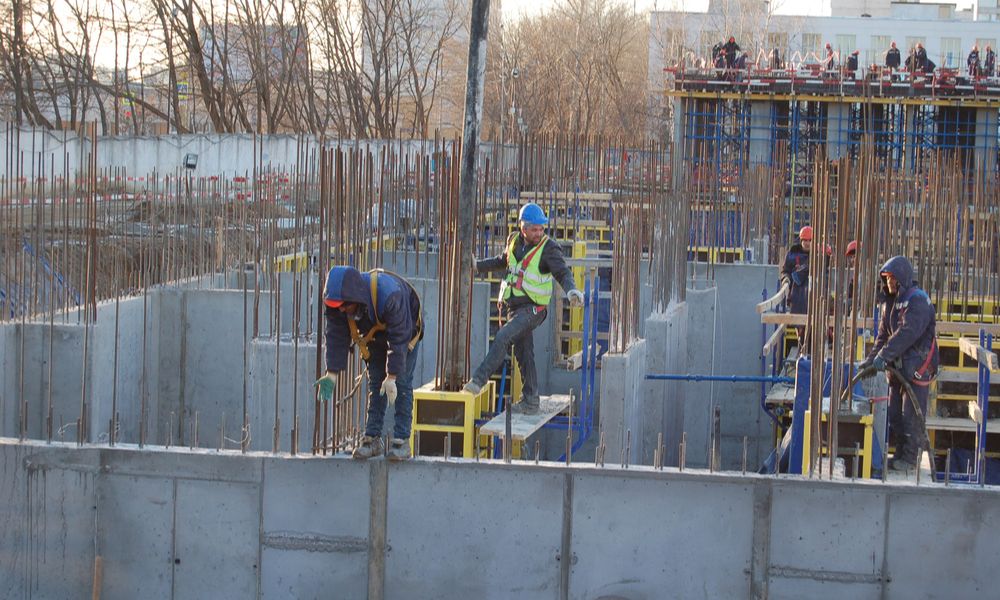
Step-by-Step Guide to Quantity Takeoff for Complex Structures
Performing a detailed and accurate quantity takeoff for complex structures requires a structured approach. Here’s a step-by-step guide to ensure you cover all the critical aspects:
Step 1: Gather and Review Project Documents Thoroughly
Start by collecting all relevant documents, including architectural drawings, engineering plans, and project specifications. Reviewing these documents provides a clear understanding of the project’s requirements.
- Confirm Document Versions: Ensure you’re working with the latest project plans to avoid discrepancies.
- Understand Project Scope and Components: Familiarize yourself with the building systems, structural components, and finishes to identify all materials and systems that require measurement.
Step 2: Set Up Consistent Units of Measurement
Consistency in units of measurement is essential for accuracy, especially in complex structures where numerous materials and systems are involved.
- Standardize Units: Use cubic meters for concrete, square feet for flooring, and linear meters for piping.
- Align with Supplier Standards: Set units that match the standards used by suppliers to avoid issues during procurement.
Step 3: Organize Materials by Categories and Systems
Complex structures often include multiple systems, so organizing materials by categories or systems is crucial for a streamlined takeoff.
- Divide by Category: Use categories like structural, architectural, mechanical, electrical, and plumbing.
- Subcategorize by Material Type: For example, under structural, include subcategories like concrete, steel, and rebar.
Step 4: Leverage Digital Tools for Efficient Measurements
Use digital tools to measure dimensions, areas, and volumes directly from digital drawings. Digital software allows for automated calculations, which is particularly useful for large-scale, complex projects.
- Use Precision Measurement Tools: Bluebeam Revu offers measurement tools for length, area, and volume, while CostX provides 3D measurements, ideal for multi-level structures.
- Apply Layers and Filters: Organize measurements by layers or filters to focus on specific sections of the project and simplify review.
Step 5: Take Accurate Measurements for Each System
For complex structures, you’ll need to measure each system separately to account for its unique requirements. This may include structural components, HVAC systems, electrical wiring, and more.
- Measure Structural Elements: Measure beams, columns, and slabs accurately for a stable foundation.
- Document System-Specific Components: For HVAC, measure ductwork and fittings; for plumbing, measure piping and fixtures.
- Apply Count Tool for Repetitive Items: Use digital tools to count items like bolts, fixtures, and rebar sections.
Step 6: Calculate Waste Allowances
Waste is inevitable in construction, particularly for projects with intricate designs. Waste allowances help account for material losses due to cutting, fitting, or breakage.
- Adjust Waste Percentages by Material: Use a 5-10% waste allowance for materials like tiles and concrete, adjusting as needed for specific materials.
- Account for Overlap and Rework: For complex structures with intricate designs, consider additional waste factors to accommodate design changes.
Step 7: Verify and Cross-Check Quantities
Once measurements are complete, it’s essential to verify the quantities for accuracy. Cross-checking ensures all quantities are correct, preventing costly errors.
- Implement Peer Reviews: Have another team member review the takeoff sheet to catch any potential errors.
- Use Checklists for Completeness: Verify that all material types and systems are accounted for, from structural elements to fixtures.
Step 8: Update the Takeoff Sheet as Project Plans Change
Design changes are common in complex structures, so it’s important to keep your takeoff sheet up to date. Revisions ensure that quantities align with the latest project specifications.
- Regularly Review and Update Quantities: When changes occur, adjust quantities accordingly to maintain an accurate takeoff.
- Communicate Changes with Teams: Notify procurement, project management, and other relevant teams to keep everyone informed and aligned.
Best Practices for Accurate Quantity Takeoff on Complex Structures
- Use Digital Tools for Efficiency: Digital takeoff tools improve accuracy and save time, especially for large or multi-level structures.
- Organize Takeoff Sheets: Maintain a structured takeoff sheet with clear categories and subcategories for readability.
- Plan for Waste: Calculate waste allowances accurately based on material type and project complexity.
- Collaborate with Team Members: Engage with project managers, architects, and engineers to verify measurements and align on specifications.
Following these best practices ensures your takeoff sheets are detailed, accurate, and aligned with project requirements, supporting smooth project execution.
Conclusion
Performing quantity takeoff for complex structures requires a meticulous and organized approach, supported by the right tools and best practices. By using digital measurement tools, organizing takeoff sheets by category, and incorporating waste allowances, construction professionals can achieve a high level of accuracy that is essential for large-scale projects.
Keeping your takeoff sheets updated as plans change and collaborating with team members further enhances accuracy, helping to ensure the success of complex construction projects.
For construction estimators, mastering quantity takeoff for complex structures is a valuable skill that contributes to efficient resource management, cost control, and on-schedule project completion.
Build Your Takeoff Skills with Our Quantity Surveying Course
Want to excel in quantity takeoff for complex structures? Our Online Quantity Surveying Course offers comprehensive training on takeoff techniques, digital tools, and best practices. Gain the expertise you need to deliver accurate estimates and support successful construction projects.Enroll Now in Our Quantity Surveying Course and take the next step in your construction