In the world of quantity surveying, effective financial management is essential to the success of any construction project. From the outset of planning to the completion of the project, quantity surveyors play a pivotal role in controlling and planning costs, ensuring that projects stay within budget while maintaining quality standards. Two essential aspects of this role are cost planning and cost control. These terms may sound similar but serve distinct functions in construction and project management.
This guide will delve into the differences between cost planning and cost control, their individual significance in the lifecycle of a construction project, and why mastering these two aspects can lead to successful project outcomes.
What is Cost Planning in Quantity Surveying?
Cost planning is the initial stage of managing a project’s budget. It involves estimating, analyzing, and planning the financial resources required to achieve the project goals. Quantity surveyors collaborate closely with clients, architects, and engineers at this stage to determine the financial feasibility of the project. The goal is to create a realistic budget based on careful analysis of costs and to help the client make informed decisions early in the project lifecycle.
Key Objectives of Cost Planning
Setting a Realistic Budget:
The primary aim of cost planning is to establish a budget that reflects the client’s financial constraints and the anticipated costs of the project.
Early Identification of Costly Areas:
By breaking down the project into various components, cost planners can identify high-cost areas and provide options to optimize these.
Providing a Framework for Decision-Making:
With a well-defined cost plan, clients can make informed choices about materials, designs, and alternative solutions to fit within their financial parameters.
Preventing Cost Overruns:
Proactive planning can help anticipate and avoid potential cost escalations before they occur.
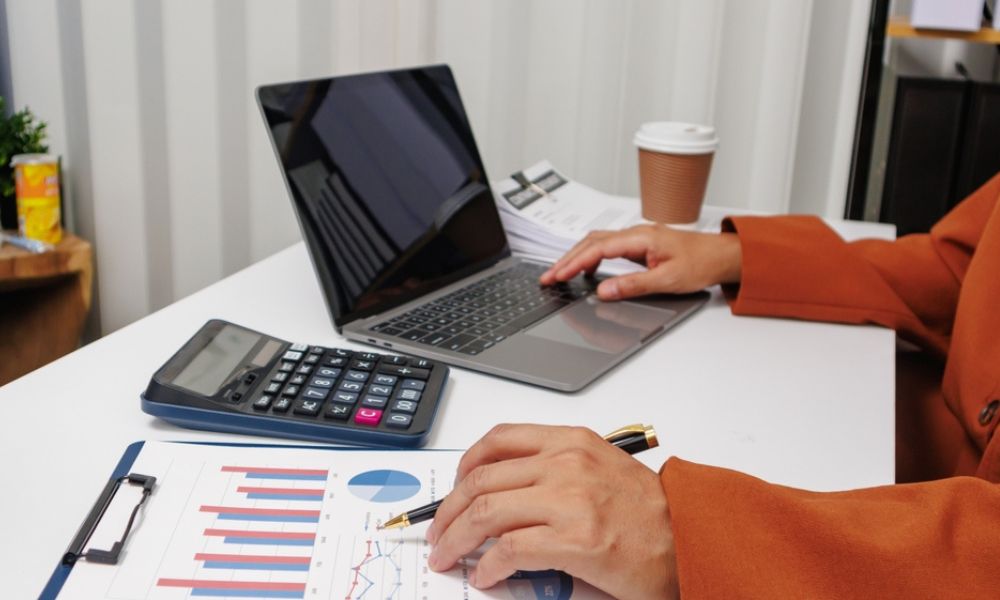
The Cost Planning Process
The cost planning process typically follows several structured steps:
Initial Cost Estimation:
This is where the surveyor calculates rough estimates based on the scope, size, and type of the project. The figures are preliminary but provide a ballpark range for budgeting purposes.
Elemental Cost Breakdown:
The project is broken down into various elements (e.g., foundations, structural works, finishes) with individual cost estimates. This process helps to pinpoint costly elements.
Cost Target Setting:
Targets are set for each element to guide future cost management. This stage often involves balancing quality and cost to meet the client’s priorities.
Re-evaluation and Adjustment:
Cost plans are adjusted as designs are refined, ensuring the budget remains aligned with the project’s evolving needs.
Benefits of Effective Cost Planning
Effective cost planning allows the project team to foresee and mitigate risks related to costs, reducing the likelihood of unexpected expenses and delays. It also builds a financial roadmap, allowing project stakeholders to navigate complex decisions with confidence.
What is Cost Control in Quantity Surveying?
While cost planning provides the framework for a project’s budget, cost control is the mechanism that ensures adherence to this budget. Cost control takes place once the project is underway and includes continuous monitoring, reporting, and adjusting costs to prevent budget overruns. Quantity surveyors use cost control techniques to identify variances and take corrective actions before issues escalate.
Key Objectives of Cost Control
Maintaining Budget Compliance:
The primary objective of cost control is to monitor expenditures against the budgeted amount, ensuring that spending aligns with the cost plan.
Identifying and Managing Variances:
As the project progresses, actual costs may differ from the planned costs. Cost control identifies these variances to determine if adjustments are needed.
Providing Transparency:
Cost control involves frequent reporting to keep clients and stakeholders updated on the financial status of the project, promoting transparency and accountability.
Optimizing Resources:
Effective cost control ensures optimal resource allocation, minimizing wastage and maximizing cost efficiency.
The Cost Control Process
Cost control is a continuous process that includes the following activities:
Regular Cost Reporting:
During the project, quantity surveyors generate regular financial reports comparing actual expenses to planned costs. These reports allow stakeholders to identify issues early on.
Variance Analysis:
When discrepancies arise, quantity surveyors analyze the cause of the variances, assessing whether they are due to design changes, unforeseen conditions, or other factors.
Corrective Measures:
Based on the variance analysis, corrective actions are taken. This might include finding alternative materials, adjusting the scope of work, or reallocating resources to stay on track financially.
Updating Cost Forecasts:
The cost forecast is adjusted continuously to reflect actual spending and any changes in the project’s scope or design.
Benefits of Effective Cost Control
Cost control ensures that projects do not exceed their budgets, enabling the project team to manage resources more effectively. Additionally, it allows clients to feel confident that their financial investment is managed responsibly, with corrective actions in place to address unforeseen cost escalations.
Key Differences Between Cost Planning and Cost Control
Timing in the Project Lifecycle
Cost Planning:
Occurs in the early stages, prior to the start of construction. It provides a financial roadmap for the entire project.
Cost Control:
Takes place once the project is underway, focusing on keeping the project within the defined budget.
Focus and Objectives
Cost Planning:
Aims to set a realistic budget and create a framework for cost-effective decisions.
Cost Control:
Concentrates on monitoring expenditures and adjusting strategies to stay within budget.
Process and Techniques
Cost Planning:
Involves estimation, elemental breakdown, and target-setting.
Cost Control:
Entails monitoring actual costs, reporting, variance analysis, and corrective actions.
End Goals
Cost Planning:
Provides a budget baseline to guide the project financially.
Cost Control:
Ensures adherence to the cost plan by addressing and managing deviations.
Understanding these differences helps quantity surveyors and project managers develop a structured approach to both planning and controlling costs, ensuring projects are completed within budget and without sacrificing quality.
The Synergy Between Cost Planning and Cost Control
While distinct, cost planning and cost control are interdependent processes. A well-prepared cost plan becomes the foundation for effective cost control. Without a realistic budget set by cost planning, cost control efforts may become reactive rather than proactive. Likewise, without vigilant cost control, even the best-laid budget plans may fail due to unforeseen expenditures.
In essence, cost planning sets the direction, and cost control keeps the project on course. Both aspects are critical in quantity surveying, particularly for projects where financial discipline and resource optimization are priorities.
How Technology Enhances Cost Planning and Cost Control in Quantity Surveying
With advancements in technology, quantity surveyors now have access to digital tools that significantly enhance both cost planning and cost control. Software applications can streamline estimation processes, automate reporting, and enable real-time tracking of expenditures. Building Information Modeling (BIM) is one such technology that has revolutionized the way cost planning and control are managed in construction projects.
BIM in Cost Planning:
BIM enables accurate 3D modeling, allowing surveyors to extract precise quantity information and estimate costs based on real-time data. This improves the accuracy of initial cost plans.
BIM in Cost Control:
Once the project begins, BIM allows surveyors to monitor progress against the plan, providing real-time updates and identifying cost variances early.
Embracing these technologies equips quantity surveyors with powerful tools to enhance cost management, making projects more efficient, transparent, and cost-effective.
Challenges and Solutions in Cost Planning and Cost Control
Even with meticulous planning and control, quantity surveyors face challenges in managing costs effectively:
Unpredictable Market Fluctuations:
Material and labor costs can fluctuate unexpectedly. Solution: Incorporate contingency allowances in the cost plan and actively monitor market trends to adjust forecasts as needed.
Design Changes: Client-driven changes during construction can disrupt budgets. Solution: Maintain an open line of communication with the client to manage expectations and approve only essential changes that align with the budget.
Scope Creep:
Expanding project requirements can lead to unplanned costs. Solution: Implement strict change management processes, requiring budget adjustments for any scope changes.
By preparing for these challenges and incorporating risk management strategies, quantity surveyors can mitigate the impact of cost variances, ensuring the project remains financially viable.
Conclusion
In quantity surveying, mastering both cost planning and cost control is fundamental to delivering successful construction projects. While cost planning sets a strong financial foundation by creating a realistic budget, cost control ensures the project remains within this budget through constant monitoring and adjustments.
Together, these processes create a harmonious approach to project management, supporting financial accountability and enhancing project outcomes.
Take Control of Your Project’s Financial Success!
Enroll in our Quantity Surveying Course Online