Last updated on December 30th, 2024 at 01:11 pm
In construction, accurate estimating is crucial for planning budgets, allocating resources, and ensuring project success. Among the many estimation methods, three commonly used techniques are Unit Cost, Assemblies, and Square Foot estimating. Each method offers unique benefits and is suited to different stages and types of projects. This guide provides an in-depth look at these estimating techniques, explaining when and how to use each one to create accurate construction budgets.
The Importance of Choosing the Right Estimating Technique
Choosing the right estimating technique can impact a project’s efficiency, cost control, and financial success. By understanding the differences between Unit Cost, Assemblies, and Square Foot estimating, estimators can apply the most appropriate method for each project phase, ultimately leading to better financial planning and risk management.
What is Unit Cost Estimating?
Unit Cost Estimating is a technique where the estimator assigns a cost per unit of measure for each work item. The unit could be square footage, linear feet, cubic yards, or any other metric suitable for the work involved. This technique is highly detailed, as it requires the estimator to define costs at the smallest unit level.
Key Features of Unit Cost Estimating
- Detailed Breakdown: Each item is broken down into units, such as per cubic yard of concrete or per square foot of flooring.
- Accuracy: Provides a high level of accuracy by specifying costs per item, helping to minimize overspending or underspending.
- Flexibility: Can be adapted to various project types, making it a versatile choice for both residential and commercial construction.
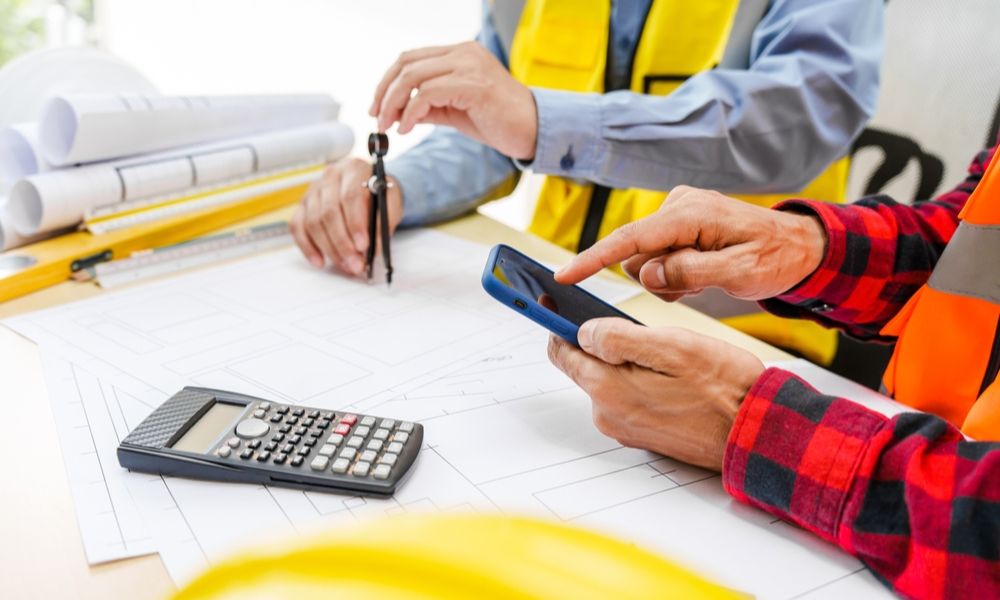
Advantages of Unit Cost Estimating
- Increased Precision: By focusing on individual units, estimators can identify exact quantities, reducing the risk of miscalculations.
- Detailed Budgeting: Offers a granular view of expenses, which is beneficial for complex projects with multiple phases.
- Adaptable for Changes: Changes in project scope or design can be reflected by adjusting unit quantities, making it flexible for modifications.
Disadvantages of Unit Cost Estimating
- Time-Consuming: The detailed nature of unit cost estimating can be time-intensive, especially for larger projects.
- Requires Experience: Estimators must be skilled at determining accurate costs per unit, which requires industry knowledge and experience.
When to Use Unit Cost Estimating
Unit Cost Estimating is best suited for:
- Detailed Planning Stages: Ideal for final budgeting when project details are fully developed.
- Complex Projects: Useful for projects with multiple, detailed elements that require specific unit costs.
- Large Projects: Necessary when accuracy is critical for budgeting and financial planning.
What is Assemblies Estimating?
Assemblies Estimating groups related tasks or materials into assemblies, estimating the cost as a package rather than by individual units. Assemblies can include components like electrical systems, HVAC systems, or roofing, where each group includes multiple related items.
Key Features of Assemblies Estimating
- Grouped Costs: Estimating costs by grouping related items, such as an HVAC system that includes ductwork, controls, and labor.
- Simplified Process: Requires fewer individual calculations by combining related items.
- Improved Efficiency: Reduces estimating time by grouping items and applying a single cost rate to each assembly.
Advantages of Assemblies Estimating
- Time-Saving: Faster than unit cost estimating, as costs are calculated by assembly rather than individual item.
- Effective for Preliminary Budgets: Ideal for early budgeting phases when precise details are unavailable.
- Reduces Complexity: Simplifies the estimation process by focusing on groups rather than individual items.
Disadvantages of Assemblies Estimating
- Less Granular Detail: Since it groups items, it may lack the detailed accuracy of unit cost estimating.
- Risk of Over-Generalization: Grouping too many items can lead to inaccuracies if specific cost details are overlooked.
When to Use Assemblies Estimating
Assemblies Estimating is ideal for:
- Early Project Phases: Works well in the design or feasibility phases when project details are less defined.
- Residential and Light Commercial Projects: Appropriate for simpler projects where general cost groupings are sufficient.
- Fast-Tracking Projects: Helpful in projects where time constraints require a quicker estimating process.
What is Square Foot Estimating?
Square Foot Estimating calculates costs based on the area of the project, typically measured in square footage. This method is commonly used in the early phases of residential and commercial projects when detailed plans are not yet available. It provides a quick, high-level estimate based on industry averages and historical data.
Key Features of Square Foot Estimating
- Area-Based Costs: Cost is estimated per square foot, with rates applied based on project type and size.
- Quick Estimate: Offers a fast estimate by focusing on overall project area rather than individual items.
- Common in Early Stages: Frequently used during preliminary budgeting to assess project feasibility.
Advantages of Square Foot Estimating
- Fast and Simple: Provides a quick cost overview without detailed itemization, ideal for feasibility assessments.
- Industry Standards: Draws on historical data and averages, allowing for easy comparison with similar projects.
- Early-Stage Budgeting: Gives clients an approximate cost range early in the planning phase.
Disadvantages of Square Foot Estimating
- Lower Accuracy: Less accurate than unit or assemblies estimating, as it lacks specific item detail.
- Dependent on Averages: Estimates rely on generalizations that may not reflect unique project features or requirements.
- Limited Flexibility: Difficult to adjust as the project scope becomes more defined, requiring a switch to more detailed estimating methods.
When to Use Square Foot Estimating
Square Foot Estimating is best suited for:
- Preliminary Planning: Used in the early stages to determine project feasibility.
- Budget Constraints: Helps provide a rough budget outline without investing time in detailed estimations.
- Comparative Analysis: Allows clients to compare costs of similar projects based on square footage averages.
Comparing Unit Cost, Assemblies, and Square Foot Estimating
Level of Detail
- Unit Cost: Offers high detail, calculating each item individually.
- Assemblies: Groups items, providing moderate detail without full itemization.
- Square Foot: Low detail, focusing on area-based estimates.
Accuracy
- Unit Cost: Highly accurate for detailed project budgets.
- Assemblies: Offers moderate accuracy, suitable for grouped costings.
- Square Foot: Less accurate, ideal for preliminary budgets.
Speed of Calculation
- Unit Cost: Time-consuming due to detailed itemization.
- Assemblies: Faster than unit cost due to grouped estimations.
- Square Foot: Quickest of the three, providing a broad estimate.
Use in Project Phases
- Unit Cost: Best for final budgeting stages.
- Assemblies: Ideal for design or early project phases.
- Square Foot: Suited for initial planning and feasibility assessments.
Choosing the Right Technique for Your Project
Selecting the right estimating technique depends on the project’s complexity, phase, and available information:
- Unit Cost is ideal for projects requiring precise budgeting and detailed costs. This technique is best used in the final budgeting stages when project specifics are clearly defined.
- Assemblies works well in early phases, offering a balance between speed and accuracy. It’s also suitable for projects where some design elements are established, but full detail isn’t yet necessary.
- Square Foot is beneficial in preliminary phases, allowing for quick feasibility assessments. It provides clients with a rough budget range and is ideal for early-stage planning.
Conclusion
Understanding and selecting the right estimating technique is essential for accurate construction budgeting. Unit Cost, Assemblies, and Square Foot estimating each serve different project needs and phases, ensuring that estimators can create reliable budgets from project conception through to completion.
By choosing the most appropriate technique, estimators can enhance accuracy, improve efficiency, and better manage project costs.
Want to Master Estimating Techniques?
Looking to expand your estimating skills? Enroll in our Quantity Surveying Course Online and learn the ins and outs of estimating techniques like Unit Cost, Assemblies, and Square Foot. This comprehensive course is designed to help you build accurate budgets and make informed decisions for every project phase.